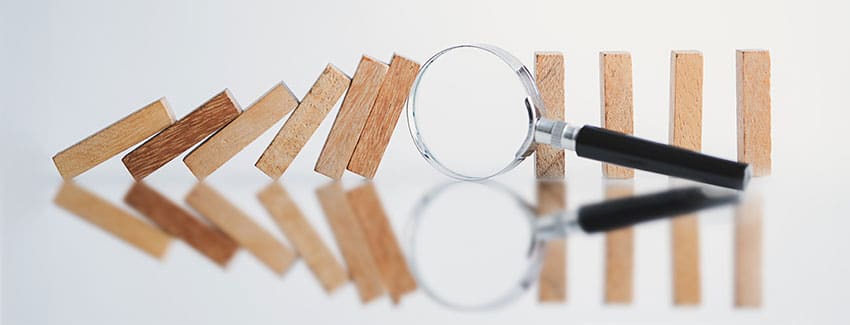
In my previous Food Quality Food and Safety Insights Blog post, I discussed the importance that risk assessment plays in manufacturing safe and high-quality food products. By employing the Risk Assessment techniques, the manufacturing processes are continually improved. When a process fails or does not work in the intended way, a Corrective and Preventive Action (CAPA) program is utilized to find a root cause, develop a corrective action to get the process moving again safely, as well as developing preventive actions that permanently correct the issue so that this and other related processes do not fail in the future.
A Corrective and Preventive Action (CAPA) program is required by Global Food Safety Initiative (GSFI) certifying bodies. The value of this program is not only in compliance, but to provide a portion of continuous improvement through an organization, specifically to continue to improve processes to manufacture safe and quality foods.
The process of conducting a CAPA is best done with a diverse team. While it may seem unusual to have a team that includes members that are not directly involved, such as having a member of HR on the team for an issue in operations, but it provides a unique, outside perspective that may not be seen by those too close to the problem. Once the team is developed, a clear definition of what happened in the specific issue as well as details on larger issues that may fail in the same way. Once the issue is clearly defined, the team can begin a root cause analysis.
While there are many established processes to conduct a root cause analysis, Tree Top has decided to universally use the 5-Why technique. The best way to describe a 5-Why process is to become the toddler and continually ask and answer the question “Why?” beginning with the scenario and move through the analysis from there. This is usually done 5 times, thus the name “5-Why”, but it can be less or more, just as long as a true root cause is reached. You will know it is the true root cause when there is no further “Why” that you can ask and get a productive answer.
Here is an example I ran through for a practice/training CAPA:
The fictional problem statement for this is:
Due to going 10 mph over the posted speed limit (traveling 45-mph in a 35-mph zone) I got a $300 ticket on 7/15/2020 at 7:00 am.
The first question in the 5-Why is:
Why was I going 10 mph over the posted speed limit (traveling 45-mph in a 35-mph zone)?
To this the answer is:
I was speeding through town to get to work on time.
Then the next Why is:
Why was I speeding through town to get to work on time?
Answer:
I left my house late which required me to drive faster to get to work on time.
Question:
Why did I leave my house late, thus requiring me to drive faster to get to work on time?
Answer:
I woke up late, so I couldn’t leave the house earlier.
Question:
Why did I wake up late?
Answer:
My alarm clock did not go off to wake me up.
Question:
Why didn’t my alarm clock go off to wake me up?
Answer:
I forgot to turn my alarm clock on Sunday night before I went to bed.
Last question:
Why did I forget to turn on my alarm clock Sunday night?
Last answer:
My alarm is not automatic to turn off on the weekends and on on the weekdays, I did not remember to set my alarm Sunday night.
The last answer statement is the root cause, or what the root cause is derived from. Here in this example it is clear that if I had an alarm clock that automatically turned on and off depending on the weekdays and weekend days, I would have not gotten a speeding ticket. (By the way, this is fictional, and I have never gotten a speeding ticket for not waking up early.)
To bring this back to the food industry, this 5-Why Root Cause Analysis Technique can be applied to all investigations to lead back to a root cause, including mechanical failures that may be due to poor or lacking preventive maintenance, out of specification products due to manufacturing inadequacies, to find the root causes to audit non-conformances, etc. When something does not work, or failures are sporadically happening, finding a true root cause is crucial to preventing the same issues from continuing to plague the processes.
Next month I will walk through the process of taking the root cause and working through making effective and successful preventive actions. I will also be discussing the difference between a Corrective Action and a Preventive Action.
Our quality team is here to support your food safety questions. Please feel free to email me at Kristine.mcdonald@treetop.com.
For more information about Tree Top’s fruit ingredients, explore our product pages.